Painting and drying linef for pump valve and VOC catalytic combusion device
Shanghai Liangshi designed and manufactured a pump-type valve through the environmentally-friendly spray drying production line for a valve company in Shanghai. The environmentally-friendly spray drying production line system includes a suspended conveyor line, an environmentally-friendly dry spray booth, an environmentally friendly flow chamber, and a gas. Heating and drying device, trolley oven, paint booth and fixture room, VOC organic waste gas catalytic combustion device, automatic electrical control system, etc. The whole through-type spray drying production line electrical appliances and fans are equipped with explosion-proof devices and accessories dry powder fire extinguishing devices to ensure that the spray drying production line is environmentally safe and stable.

Pump valve environmentally friendly spray drying production line
The pump valve spraying and drying production line VOC processing device adopts an environmentally-friendly and efficient honeycomb activated carbon adsorption concentrated catalytic combustion organic waste gas treatment device, and the honeycomb activated carbon adsorption concentrated organic waste gas catalytic combustion device utilizes high-performance second-generation activated carbon material honeycomb activated carbon as adsorption concentrated material. Under the action of a precious metal catalyst with honeycomb ceramics as a carrier, the organic matter is converted into a relatively harmless substance such as carbon dioxide and water, and a low-energy, high-efficiency VOC organic waste gas treatment device automatically controlled by PLC.
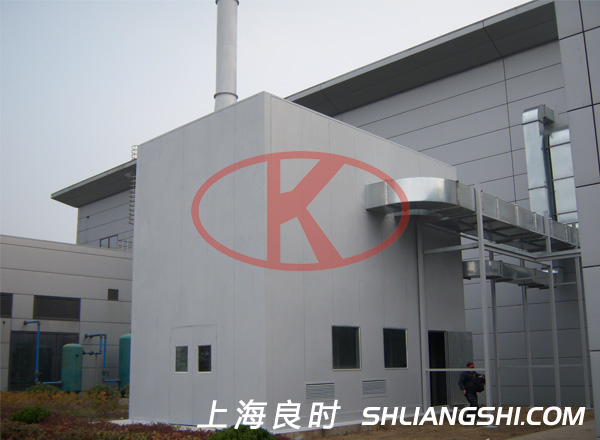
Honeycomb activated carbon adsorption concentrated organic waste gas catalytic combustion device
Honeycomb activated carbon adsorption concentrated catalytic combustion of VOC organic waste gas treatment device, using honeycomb activated carbon with less wind resistance as adsorbent material, the organic components in the paint organic waste gas are absorbed to the standard discharge. The adsorption bed is generally arranged in two or more, and is used alternately. When the organic matter adsorbed by one adsorption bed reaches a predetermined adsorption amount (concentration limit), it is transferred to the desorption regeneration process, and at the same time, another adsorption bed starts to perform adsorption purification. Desorption is the use of a desorption fan to make the adsorption bed and catalytic combustion equipment a closed loop system. The hot air generated by the catalytic combustion device is first introduced into the adsorption bed to be desorbed, the adsorbed organic matter is desorbed, and then introduced into the catalytic combustion device to perform catalytic oxidation in the catalytic combustion chamber to eliminate organic matter in the organic waste gas stream. The heat released by the catalytic combustion of the organic matter is sufficient to maintain the temperature of the catalyst bed, and the organic matter is efficiently purified. The hot gas discharged from the exhaust gas is partially used for the desorption regeneration of the adsorbent adsorbent, and the remaining heat can be introduced into the drying room for reuse. The use of waste heat. Through the process control, the concentration of organic matter in the degassed gas stream can be increased by more than 10 times compared with that before the adsorption operation, and the gas flow rate is only about 1/10. Through the combination of the above two purification processes, the organic exhaust gas emissions of large air volume and low concentration paint are changed into small air volume, medium and high concentration organic waste gas treatment, and the heat energy generated by catalytic combustion of organic substances is effectively utilized, so the running cost is low.